Manufacturers need to make real-time, data-driven decisions to ensure efficient operations and first-class customer service. Yet many organizations still rely on spreadsheets or outdated planning tools MRP (Material Requirements Planning).
Supply chain planning driven by mathematical optimization is fundamentally different from traditional planning methods and simpler heuristic calculations that are often known as optimization. Mathematically optimized planning allows manufacturers to respond swiftly and confidently to changing conditions and maximize supply chain performance.
This whitepaper illustrates how mathematical optimization works as one of the key capabilities in a strong supply chain planning solution —and how organizations can use it to streamline operations and maximize profits.
Why do you need optimization?
Optimization software can transform the way companies plan and manage their supply chains. It offers several distinct advantages over traditional planning methods, which often focus on scaling process and decision-making with heuristics.
Feasible plans
Supply chain planning and optimization software takes a different, more realistic approach than other methods like MRP, which assumes infinite capacity and material availability. System-generated plans factor in supply chain costs and constraints up front, making them more feasible out of the box. Optimized plans seldom require manual adjustment and fine-tuning, shortening the gap between planning and execution.
System-generated plans factor in supply chain costs and constraints up front, making them more feasible out of the box.
Profit optimization
Optimization software always returns the plan that best meets the company’s overall business objectives: typically, maximum profit. This is possible because the system evaluates and optimizes the complete supply chain as a single entity, recognizing the cost associated with each activity.
Planning speed
Lightning-fast optimization algorithms allow planners to generate fully optimized plans in seconds. As a result, the organization can always work towards up-to-date plans based on the latest inputs.
Scenario planning
The system’s speed also allows planners to quickly simulate and assess the impact of different scenarios before making important planning decisions.
How does supply chain optimization work?
There’s no need for the average user to grasp the inner workings of mathematical modeling and optimization techniques. That said, it’s helpful for planners and business users to have a basic understanding of the system architecture to establish trust in the process and its results.
Let’s dig deeper into the main components of a supply chain optimization solution and how they impact broader business operations:
1. A supply chain digital twin
A supply chain digital twin is a virtual replica of your physical supply chain. It provides the blueprint for the planning solution and is stored in an in-memory database for instant access and quick processing.
A digital twin models a company’s supply chain processes and resources, including associated costs and constraints. Factories, production lines, machines, tools, warehouses, vehicles, and staff are all represented here. Think of it as an advanced simulation of the entire supply chain that receives regular data updates from numerous sources, helping to determine how goods and information flow within the system.
2. Data requirements
The solution needs access to accurate, up-to-date information from your existing business systems.
Most of the required data can be sourced from the ERP system. However, interfaces to Product Lifecycle Management (PLM) Customer Relationship Management (CRM) Transportation Management, and Warehouse Management systems may also be necessary.
Examples of required information include:
- Sales forecasts
- Customer orders
- Product master data
- Stock levels
It is important to have a flexible solution that can interface to any and every potential data source.
3. Mathematical optimization
Problems with multiple variables are difficult to solve without mathematical optimization. An optimization solution uses multiple algorithms and solvers in combination to maximize the defined objective. It does so while considering the constraints outlined by the supply chain digital twin through the input data.
These constraints include (but are not limited to):
- Sourcing and procurement. This task involves optimization of the procurement plan, including supplier selection, order quantities, and order frequencies.
- Manufacturing. This activity involves optimizing production plans, including outsourcing options and detailed production schedules.
- Inventory. The business rules engine establishes adaptive safety stock levels and other inventory parameters.
- Distribution. This task involves the optimization of shipping routes, mode selection, and delivery schedules.
Most commonly, the objective is either maximum profit or maximum customer service at the lowest cost. It is also possible to optimize for other factors, such as lowest CO2 output.
Regardless of which option a business chooses, the solution will find the optimal overall option for the business while considering preset rules, costs, and constraints.
4. User interface
The user interface is designed to maximize planner productivity. It separates the end-user from the complexity of the mathematical modeling and calculations that take place behind the scenes.
Configurable dashboards and visualization tools support the planner’s work, and users can easily monitor KPIs and track the progress of their optimization efforts.
The system issues real-time alerts, exceptions, and notifications to inform users of critical events or deviations from the optimized plan. Planners can then choose to address the issues manually or leverage the system’s “what-if?” simulation capabilities to explore options and ensure they make the right business decisions.
Workflow tools ensure that planning processes and communication protocols are followed. Additionally, planners can aggregate information with ease to get a complete overview of the supply chain because there’s only one source of planning data. They can also drill into the data to determine the root cause of specific issues.
To find the optimal plan, we first need to define the planning problem and the parameters framing it. Once a digital model of the supply chain is in place, the mathematical optimization algorithms can go to work.
Optimization examples
To better understand the difference between supply chain optimization and MRP, let’s examine how each system tackles two common planning challenges.
Example 1: Product mix
In the first example, we take a closer look at how the system uses mathematical modeling to optimize a planning problem.
The scenario is a bakery that wants to determine an optimal product mix. To keep it simple, we consider two products, bread and brownies, and two ingredients, flour and sugar.
Optimizing the product mix with optimization
The flour supply is limited to 50kg for the period. The planning system accesses the products’ bills of materials and sees that a loaf of bread requires 1kg of flour and a brownie ½ kg. The graph below shows the possible product mix given the flour constraint.
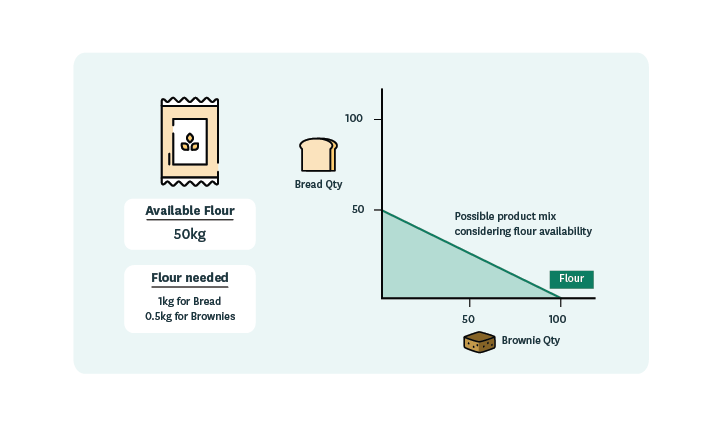
After adding a supply constraint for sugar, the possible product mix looks as follows.
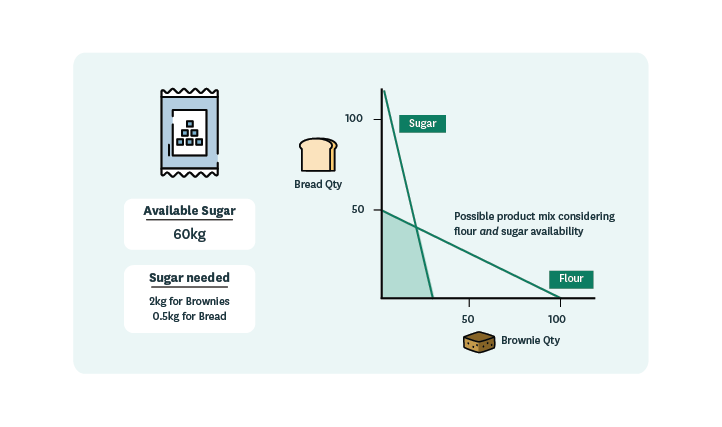
Next, the demand forecast is considered. We don’t want to produce more than what we have demand for (45 breads and 25 brownies), so the possible product mix is further reduced.
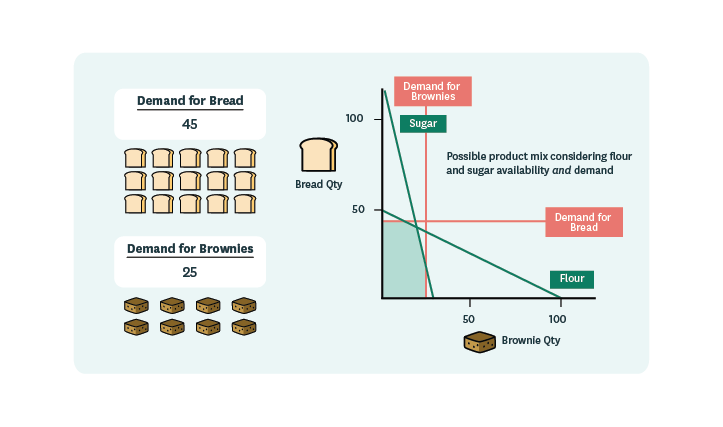
The optimal product mix is where the bakery achieves maximum profit. With a profit contribution of $1.50 for bread and $2.00 for brownies, the system has all the information it needs to determine the optimal mix.
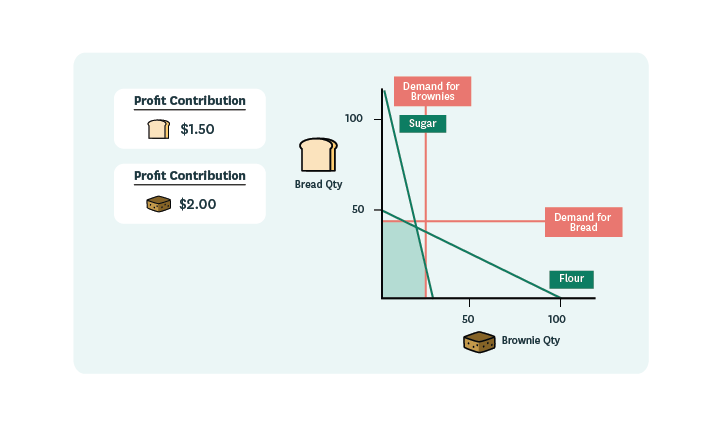
In this example, a Linear Programming (LP) algorithm is used to determine the optimal product mix. The system establishes the profit contribution line and finds the optimum. Remember – all this happens automatically!
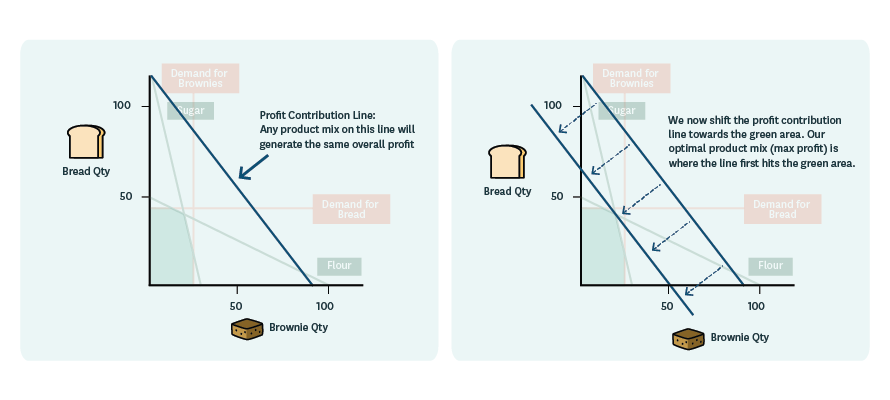
The optimal product mix is 40 breads and 20 brownies.
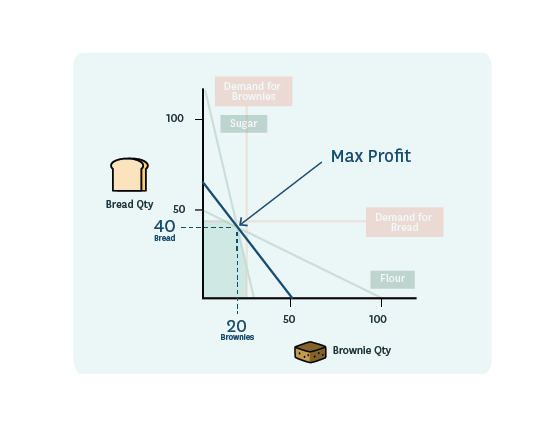
The above example is conveniently simple, but the beauty of mathematical optimization is that you can achieve the same optimized results for even the most complex supply chains. The algorithms can optimize the production, storage, and distribution of thousands of products competing for constrained materials and resources in a matter of seconds.
Optimizing the product mix without optimization
Without optimization, a plan would have assumed a limitless supply of flour and sugar. It’s only afterward that constraints can be added, requiring the manual intervention of a planner.
Example 2: Stock build
Companies dealing with seasonality or big promotions need to find the best way to build stock ahead of a peak in demand.
There are two basic strategies: gradually build up the required stock over time or add extra capacity closer to the peak.
With the gradual stock-build approach, you maintain a steady and cost-efficient production schedule and can take advantage of any spare capacity. However, because it involves holding stock for longer, storage and handling costs will be higher. There is also an increased risk of product expiration and obsolescence with this strategy.
The diagrams below illustrate how inventory is gradually built by maintaining a constant line utilization (40 units per week) in anticipation of a demand peak during weeks 28 to 32.
Stock build over a longer time period
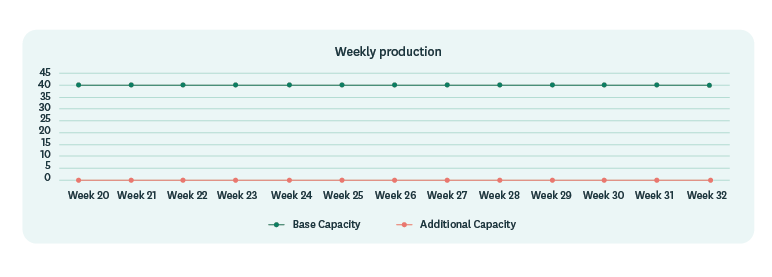
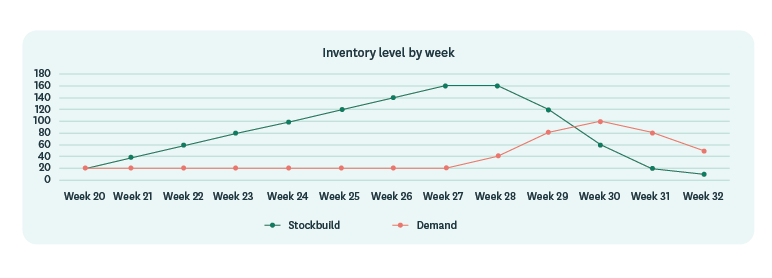
The alternative is adding more production capacity closer to the peak in demand. This can be achieved through adding extra shifts, re-deployment of in-house capacity, or by using outsourcing partners.
Building closer to the peak keeps inventory levels and inventory-related costs low. However, adding short-term production capacity usually comes at a premium, if it’s an option at all.
Stock build using extra capacity closer to peak in demand
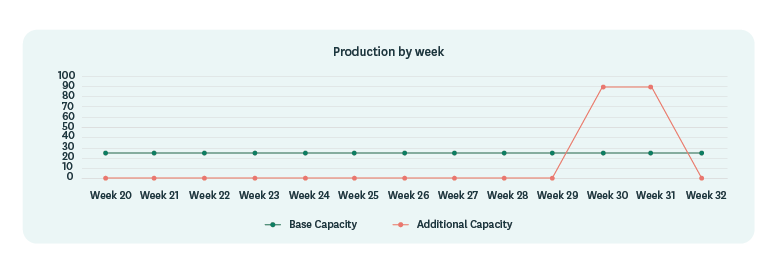
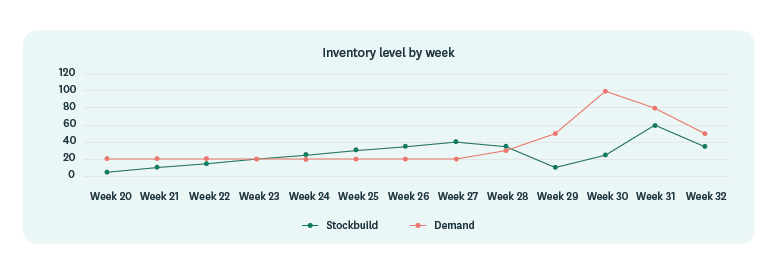
The graphics above show the difference between the two alternatives. But how can you tell which option is best? It could even be a combination of the two options.
If you look at a single product in isolation, this is not a complex problem. More realistic scenarios often involve hundreds or even thousands of products competing for production, storage, and distribution capacity across multiple sites. In these cases, the optimal solution is seldom obvious and could surprise even experienced planners.
Planning the stock build with optimization
Planning in a world of finite resources and seemingly infinite disruption always involves tradeoffs. A supply chain optimization solution will identify the stock build strategy that best satisfies your overall business goals, whether to maximize overall profits or meet customer service targets at the lowest possible cost.
As long as the mathematical solver has access to the data that frames the planning problem, it can perform the necessary optimization. Because the mathematical solver considers the entire supply chain, the planner doesn’t have to instruct the system to build stock. The system handles this automatically as part of meeting the optimization objective.
In this example, the supply chain model defines the costs and constraints relating to overtime, cost of capital, product expiry, batch sizing, product mix, and more. When combined with demand and stock on-hand information from 3rd party systems, the solver has everything it needs to calculate the optimal plan.
Planning the stock-build without optimization
Planning the same stock build using an ERP system’s MRP and distribution requirements planning (DRP) functionality is an entirely different challenge.
Unable to factor in costs and constraints, MRP and DRP must make a series of assumptions, including infinite capacity and fixed production and distribution lead times. However, capacity is rarely unlimited, and lead times are not fixed per definition. Instead, they depend on the availability of materials and production, storage, and distribution capacity. As a result, MRP-generated plans are of much lower quality, and the planner is left with a lot of work to validate the plan’s operational feasibility.
MRP’s inability to deliver a plan that can be executed “out-of-the-box” is only part of the problem. Because MRP doesn’t consider the cost and overall profitability of the plan, it’s almost impossible to determine if the plan meets a company’s commercial goals.
Changing the role of the planner
As a planner, working with a supply chain optimization solution is very different from using an MRP system (without mathematical optimization).
With MRP, planners can see when there’s an issue but are left to figure out how to fix it themselves. This is time-consuming, and important planning decisions risk being based on gut feeling rather than real-time data and facts.
Creating an entirely feasible and commercially optimized plan with supply chain optimization software is almost instant. Whether preparing different planning scenarios for the monthly S&OP cycle or addressing an immediate production issue, planners can add more value to the organization.
With a system that models and optimizes the entire supply chain, planners and business stakeholders have complete visibility of all planned activities and how they interrelate. If an aspect of the plan changes, any ripple effects are immediately visible. This allows for faster decision-making and higher-quality decision-making.
The six biggest ways optimization impacts the role of a planner include:
- Improved planning automation means more time to focus on exceptions.
- Improved supply chain visibility analytical capabilities allow planners to identify and address supply chain issues before they become problems.
- The plans can be executed “out-of-the-box” with little or no need for manual adjustment.
- The speed of the optimization algorithms allows planners to run multiple what-if analyses before making important decisions.
- The planner will maintain the “digital twin,” keeping business rules, costs, and constraints up to date.
- Typically, the planning function will become more strategic as trust grows. This can include a more central role in the company’s Sales & Operations Planning (S&OP) or Integrated Business Planning (IBP) cycle.
How to get started with supply chain optimization
Supply chain optimization can add significant value to manufacturing and distribution companies of all sizes. Recent advances in computing technology have seen solutions become increasingly affordable and user-friendly, and businesses wanting to take advantage can do so with confidence.
The modular nature of supply chain optimization solutions means companies can start small and gradually expand the solution footprint, thereby minimizing project risk and cost. RELEX recommends first targeting the planning areas where the technology will add the most value. This is why many companies choose to address their longer-term production and inventory planning before moving on to shorter-term production scheduling.
Ultimately, supply chain planning based on mathematical optimization has the power to transform your business — especially when used as one of several tools in a company’s supply chain planning toolbox. Any manufacturing or distribution organization not yet using the technology should find out what it would mean for their customer service and bottom line.